Waste Management
Challenges and Commitments
GGC strives to reduce waste quantity and efficiently manage both hazardous and non-hazardous waste in the production process to lessen environmental impacts and resource shortages as well as help to reduce the Company’s costs relating to waste management.
Key Stakeholders
Employee
Community
Shareholder, Investor and Analyst
Government
Supplier and Business Partner
Customer
Goals
that goes to the landfill to
zero
Management Approach
Waste Management Guidelines
GRI 306-1 (2020), GRI 306-2 (2020)
The company is committed to minimizing the generation of both hazardous and non-hazardous waste arising from production processes, maintenance activities, and other organizational operations. This effort aims to maximize resource efficiency throughout the value chain and reduce waste generation to the greatest extent possible, while also preventing and mitigating potential impacts on surrounding communities and the environment .
Waste management begins at the source and extends through every stage of the company’s production process. The company implements an efficient waste management system based on the principles of the Circular Economy and in alignment with international standards. It also incorporates the 5Rs approach to waste reduction: Reduce (minimizing waste generation), Reuse (extending the life of materials), Recycle (recovering resources), Refuse (avoiding the use of environmentally harmful substances), and Renewable (prioritizing low-carbon and renewable energy use). These efforts are complemented by a green procurement policy.
This policy underscores the company’s strong commitment to reducing waste generation and minimizing landfill disposal.
3Rs Principle
GGC has established an action plan to control, inspect, and monitor waste management. It begins with collecting, storing, and transporting waste generated from the Company's activities to be delivered to the treatment and disposal facility certified by the Department of Industrial Works in accordance with the Ministry of Industry's announcement on the disposal of sewage or unused materials. The Company, then, arranges for tracking and reporting of waste information through the waste transport supervision system every time.
Waste Management Programs
GGC places strong emphasis on both security and environmental sustainability, particularly regarding industrial waste generated from its production processes. The company manages waste in alignment with the 5Rs principles: Reduce (minimizing waste generation), Reuse (reusing materials), Recycle (recovering resources), Refuse (avoiding substances that harm natural resources and the environment), and Renewable (utilizing low-carbon, renewable energy sources).
GGC conducts regular monitoring and analysis of waste to identify its sources within production processes and supporting activities. The collected data is used to determine the root causes of waste generation and to explore potential improvement opportunities, whether through reducing volumes, reusing materials, or modifying production processes. These efforts support the company’s ongoing goal of achieving Zero Landfill, minimizing the need for waste disposal through landfilling.
GGC has developed a comprehensive waste management action plan covering both regular operations and maintenance periods. The plan is guided by the 5Rs environmental culture—Reduce, Reuse, Recycle, Refuse, and Renewable—to promote efficient resource use and minimize waste requiring disposal. Key approaches include:
- Solid Waste Reduction in Productions: GGC has improved its production processes to prevent waste generation at the source. This includes the segregation of reusable waste materials from non-reusable ones, along with the provision of designated areas and containers for efficient storage and separation. For example, insulation materials removed from equipment are carefully sorted and stored to enable future reuse. This approach helps reduce the volume of waste requiring disposal and supports more sustainable resource management.
- Waste Valorization: GGC collaborates with waste management partners to utilize non-hazardous waste as a feedstock in the biogas production process. This effort not only reduces the amount of waste generated but also promotes the use of environmentally friendly alternative energy, contributing to both resource efficiency and sustainable energy development.
- Equipment and Machinery Optimization: GGC has analyzed and improved the selection of materials and equipment used in the production line to ensure suitability for their specific functions. This helps extend the service life of machinery, reduce the likelihood of waste from wear and degradation, and minimize unplanned downtime. In addition, a systematic cleaning schedule has been established during maintenance shutdowns to prevent the accumulation of waste, further enhancing operational efficiency and sustainability.
- Improvement in Chemical Usage Practices: GGC has studied and tested the use of alternative chemicals that are safer and more environmentally friendly for equipment cleaning processes. Guidelines and procurement requirements for chemical use have been established to align with the company’s policy on reducing hazardous chemical usage. This initiative supports safer operations and minimizes environmental impact.
Contractor Safety Commitment for GGC Plant Shutdown 2024
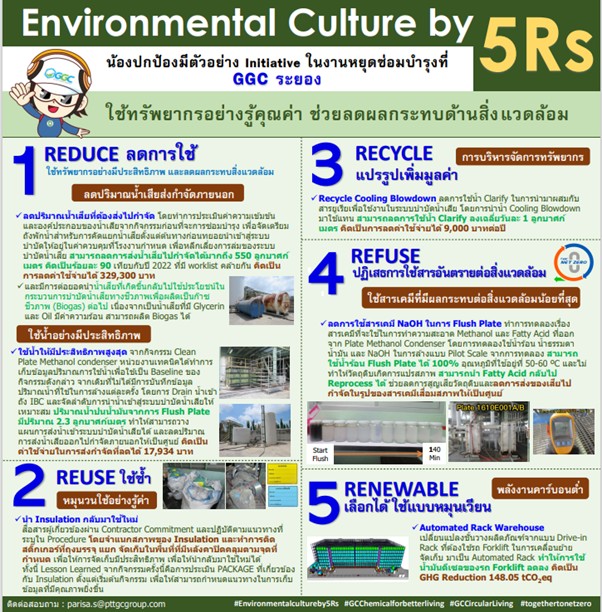
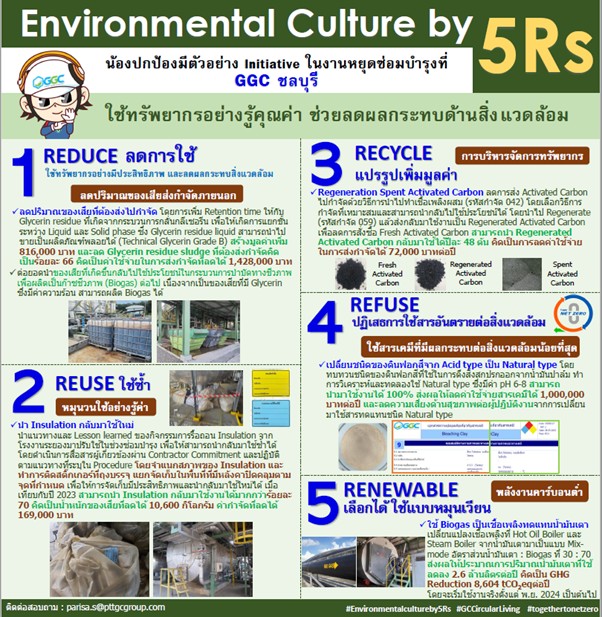
For More details about our waste management performance, see GGC Performance Data 2024
For more about our waste management projects, see the 2024 Integrated Sustainability Report at Integrated Sustainability Report 2024.
1. Waste to Biogas
The Waste-to-Biogas project involves converting waste and wastewater generated from GGC’s glycerine production process into biogas, which is then used as an alternative energy source for steam generation. This initiative helps reduce the use and import of conventional fuels, such as fuel oil.
Beyond turning waste into a valuable resource and supporting the company’s goal of achieving zero hazardous and non-hazardous waste to landfill, the project also contributes to lowering waste transportation and disposal costs, as well as reducing GGC’s energy procurement expenses.
2. Reduce wastewater from maintenance activities project
The project to reduce wastewater volume from maintenance activities applies the "Reduce" principle by minimizing the amount of wastewater requiring external disposal. Before maintenance begins, the company assesses the concentration and composition of the expected wastewater. Based on this assessment, dedicated holding tanks are prepared to segregate wastewater at the source. This enables a gradual and controlled introduction of wastewater into the treatment system, ensuring compliance with the factory’s discharge limits and preventing system overload or failure.
As a result, the volume of wastewater requiring off-site disposal was reduced by up to 550 cubic meters, representing a 90% reduction compared to similar activities conducted in 2022.
3. Water Efficiency from Clean Plate Condenser activity
The project to maximize water efficiency from the Clean Plate Methanol Condenser activity applies the "Reduce" principle. The company collected data on water usage to establish a baseline for this activity. Wastewater was directed into IBC tanks for temporary storage, and the discharge into the wastewater treatment system was carefully scheduled to ensure optimal load distribution.
The cleaning process generated approximately 2.3 cubic meters of oily wastewater. This approach allowed the company to plan the wastewater treatment process more effectively and enhance overall efficiency in water management.
4. Reduce the volume of glycerin residue (sludge) requiring disposal Project
The project to reduce the volume of glycerin residue (sludge) requiring disposal involved improving the waste management process for glycerin residue generated during the glycerin distillation process. GGC extended the retention time to promote clearer phase separation between the liquid and solid components.
As a result, the liquid portion with suitable characteristics could be recovered as a by-product in the form of Technical Glycerin Grade B, which is marketable. This measure not only reduces the volume of waste requiring disposal but also adds value to the waste, supporting the company’s goal of achieving zero waste to landfill.
5. Increase Time for Backwash Side Stream Filter project
The Increase Time for Backwash Side Stream Filter project applies the principles of Recycle and the use of low-carbon, renewable energy. The objective of this initiative is to reduce the volume of clarified water used as make-up water in the cooling water system.
By extending the operating time of the side stream filter, which began in January 2024 and continues to date, the company successfully reduced the use of clarified water by 1,747.40 cubic meters. This project not only supports more efficient water resource use but also aligns with GGC’s sustainability goals.
6. Recycle Cooling Blowdown project
The Recycle Cooling Blowdown project applies the Recycle principle by replacing clarified water with cooling blowdown water in the urea mixing process used in the wastewater treatment system. This substitution has resulted in an average daily reduction of 1 cubic meter of clarified water usage, contributing to more efficient water resource management and supporting the company’s sustainability efforts.
7. Regeneration of Spent Activated Carbon project
The Regeneration of Spent Activated Carbon project applies the Recycle principle by selecting an appropriate disposal method that allows for beneficial reuse. Instead of disposing of used activated carbon, the company sends it for regeneration and reuses it as Regenerated Activated Carbon, reducing the need to purchase fresh activated carbon.
This approach enables the company to reuse approximately 48 tons of regenerated activated carbon annually, supporting both cost savings and resource efficiency.
8. Reduction of Sodium Hydroxide (NaOH) Use in Plate Flushing project
The Reduction of Sodium Hydroxide (NaOH) Use in Plate Flushing project applies the Refuse principle, aiming to avoid the use of substances that are harmful to natural resources and the environment. The project focuses on cleaning methanol and fatty acid residues from the Plate Methanol Condenser.
A pilot-scale trial was conducted using hot water, ambient water, oil, and sodium hydroxide (NaOH) for flushing. The results demonstrated that hot water alone (at 50–60°C) could effectively flush the plates without altering the raw material properties. Additionally, the recovered fatty acid could be reprocessed and returned to the production line.
This initiative successfully reduces the loss of raw materials and eliminates the need to dispose of degraded chemical waste, supporting both resource conservation and environmental protection.
9. Material Improvement for Process Pipeline Project
GGC integrated the principle of Reduce, into the pipeline process that often encounters the Corrosion & Erosion incidents by changing materials used to manufacture pipes from stainless steel to PTFE-lined carbon steel in order to expand the functional life of the pipes from less than 5 years to more than 15 years. This resulted in decreasing waste generated from the pipeline process as well as reducing the cost of maintenance and operation by 900,000 Baht per one-time maintenance which is equal to 1.8 million Baht per year.
10. Project to increase efficiency of wastewater treatment with Integrated Fixed Activated Sludge (IFAS) system
GGC develops wastewater treatment systems byincreasing the ability to receive wastewater from methyl ester and fatty alcohol production plants and increasing the efficiency of reducing chemical oxygen demand (COD) in wastewater treatment systems with the Integrated Fixed Film Activated Sludge (IFAS) system.
This results in a reduced concentration of Total Suspended Solid (TSS) before the water is discharged, which reducing the amount of export of Glycerin Residue High Concentration for disposal, ultimately saving disposal costs by up to 16.3 milion THB per year. The treatment system also increases the capacity for wastewater treatment by COD Loading from 100 kgCOD/hr to 280 kgCOD/hr.
11. Reuse of Insulation Project
GGC applied the principle of Reuse by separating insulation that can be reused out of other materials, which can be only treated or disposed of. Moreover, GGC has managed a proper containers for reusing purpose, resulting in reductions in the amount of waste generated and waste disposed to landfills by 100 percent.
12. Reprocess of Fatty Alcohol (FAOH) Project
GGC applied the principle of Recycle by restoring Fatty Alcohol (FAOH) materials that are in transitional grades to the production and fractionation processes in order to use them as materials to produce new products. This resulted in 296 tons of FAOH being brought back into production.
Zero Waste to landfill
GGC reports the volume of waste generated from both of its plants to the Department of Industrial Works (DIW) annually. This reporting is based on the official notification issued by the DIW, which grants permission to transfer waste or unused materials outside the factory premises.
In 2024, GGC reported zero waste from its production processes being disposed of through landfilling. In addition to complying with regulatory waste reporting requirements, GGC continuously monitors, analyzes, and evaluates the volume of waste generated to identify opportunities for process improvement , apply appropriate technologies, and adopt environmentally friendly waste management practices.
The company’s goal is to reduce waste generation at the source and increase the proportion of waste that is reused or repurposed. This approach drives the organization toward more efficient waste management and supports long-term environmental sustainability.
Waste Management Training
GGC places strong emphasis on continuously building the capacity and awareness of its employees, recognizing that a clear understanding of effective waste management is a key factor in achieving the company’s “Zero Waste to Landfill” goal.
To ensure employees are well-informed and capable of managing waste efficiently, GGC has systematically integrated waste management topics into various training programs at both the organizational and departmental levels. Key training formats include:
a) Training in accordance with ISO 14001 environmental management standards
b) SHE Refresh Training conducted by the Quality, Safety, Occupational Health, and Environment Department
c) Pre-maintenance training sessions to communicate waste management procedures during plant shutdowns
d) Specialized training related to specific production processes
The core topics covered in GGC’s waste management training include:
a) Fundamental knowledge of waste types and waste management practices
b) Awareness-building and fostering a mindset of waste reduction
c) Commitment to safety, particularly for contractors
d) Enhancing resource efficiency through optimal utilization
e) Reducing waste from production processes by improving work procedures
f) Proper management of hazardous and non-hazardous waste in compliance with legal and environmental standards
These training programs not only promote a deeper understanding of waste management but also help establish sustainable practices that minimize environmental impact throughout the company’s production processes.